Key Takeaways
- Steel production hits a plateau: Steel production growth has slowed down since 2020 reflecting China’s economic downturn.
- Decarbonization drives industry change: With 7-9% of global emissions attributed to steel, the industry is under both economic and regulatory pressure to adopt greener practices.
- Industry shifts to green technologies: Transition from Blast Furnace to DRI, increased use of recycled steel, and massive deployment of renewable electricity are central to the industry’s decarbonization strategy.
- Global trade dynamics will predictably change: The move towards green steel could alter global trade patterns, particularly for regions dependent on imports like the EU.
The steel industry is one of the most significant contributors to global greenhouse gas (GHG) emissions, responsible for approximately 7-9% of the world’s total carbon emissions [9]. This sector, while vital to various industries such as construction, automotive, and manufacturing, has long been a focus of environmental concerns due to its high carbon intensity.
Steel Production and Its Environmental Impact
Globally, the steel industry produces approximately 1.9 billion tons of steel annually, a figure that has been growing at a compound annual growth rate (CAGR) of around 3% over the 2000-2020 decade (but has stabilized to 0.6% since 2020) [10]. This growth is driven primarily by demand in key sectors such as building and infrastructure, which accounts for about 52% of steel usage, followed by mechanical equipment at 16%, and the automotive industry at 12% [10].
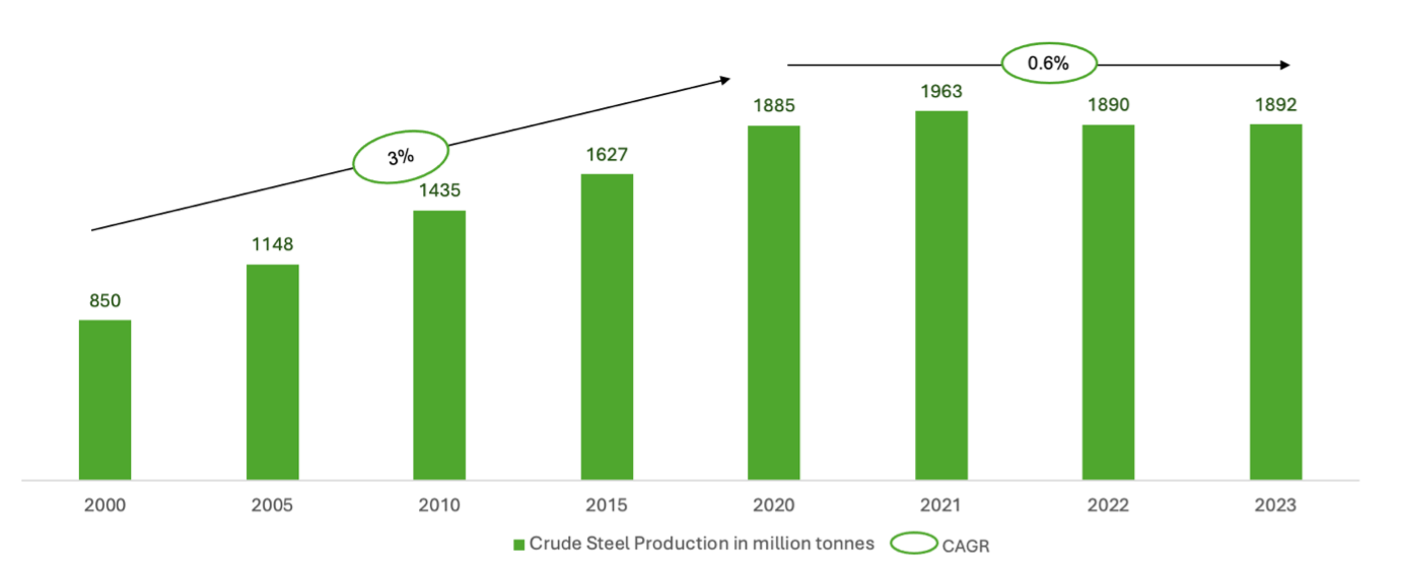
Fig. 1 Global crude steel production through 2000-2020 and for 2021, 2022, and 2023 showing the CAGR
China alone consumes 1354.2 kg/capita of steel and is the largest exporter at 83.2Mt as it produces far more steel than it consumes domestically showing its massive production capacity, supported by abundant raw materials. In comparison the European Union’s steel use per capita in 2023 was 284,3 kg. It is, notably, the largest importer at a net of 22 Mt. Transitioning to green steel is likely going to change the dependency of the EU on imports, reducing its carbon footprint and possibly increasing production costs.

Fig. 2 Comparing China and EU’s current consumption, and the stark parity in the direction of their steel trade dynamics.
The iron and steel sector emits 2.6 Gt CO2e annually, which is 7% of the global emissions from energy use and 7–9% of global anthropogenic CO2e emissions—the highest among heavy industries [18]. Weighted average carbon footprint of steel is 1.85 tons CO2 to 1 ton steel produced.[19] It is the weighted average of the two primary methods for producing virgin steel – The Blast Furnace-Basic Oxygen Furnace (BF-BOF) route and the Direct Reduction Iron paired with an Electric Arc Furnace (DRI-EAF). [10].
- BF-BOF Process: This traditional method relies on coal as a reducing agent, leading to higher emissions. The process can incorporate a limited amount of steel scrap, typically up to 30%, which helps reduce carbon intensity slightly [10]. The carbon intensity for Blast Furnace-Basic Oxygen Furnace (BF-BOF) ranges from 1.9 to 2.3 tCO2e per ton of steel produced.[17]
- DRI-EAF Process: This method is more flexible, allowing for the use of natural gas or even hydrogen as reducing agents, which can significantly lower emissions. Additionally, the DRI-EAF process can incorporate up to 100% steel scrap, making it a more sustainable option [4]. For gas-based Direct Reduction Iron-Electric Arc Furnace (DRI-EAF), the carbon intensity ranges from 1.10 to 1.6 tCO2e per ton. For low-carbon or green hydrogen-based DRI-EAF, the intensity can be significantly reduced to around 0.7 tCO2e per ton or even lower if 100% green hydrogen is used. [17]
Steel produced from recycled scrap in Electric Arc Furnaces (EAF), or Induction Furnaces can sometimes be of lower quality than virgin steel due to impurities like copper and tin, which are hard to remove and can affect steel’s properties. Additionally, scrap metal’s varied composition makes it difficult to achieve the consistency seen with virgin materials. Yet aAdvances in recycling technologies are improving the quality of recycled steel, making it increasingly competitive with virgin steel for various applications [5].
Levers to Decarbonize Steel Production
Decarbonizing steel production involves several strategies, each with its challenges and potential benefits:
- Changes in Production Process: There are various key innovations to consider here
- Switch from BF-BOF to DRI-EAF: Projects like HYBRIT of SSAB in Sweden, ArcelorMittal, Voestalpine in Austria, H2Green Steel and Boston Metal are pioneering this approach.
- Electrification and Electrolysis: Technologies like Molten Oxide Electrolysis (MOE) and Alkaline Electrolysis directly produce steel using electric current, potentially offering a carbon-free alternative if powered by renewable energy.
- Smelting Reduction: This method combines iron ore reduction and smelting in a single reactor, which can operate with lower carbon inputs compared to traditional blast furnace methods. Technologies such as HIsarna, developed by Tata Steel, allow direct conversion of iron ore into steel without the need for coke, significantly reducing CO2 emissions
- Increased Use of Steel Scrap: Maximizing the use of recycled steel scrap in the EAF process reduces the demand for virgin steel production, thereby cutting emissions. However, the availability and quality of scrap steel can be limiting factors [3].
- Switching to Low-Carbon Energy Sources: Transitioning from coal to natural gas, or better yet, green hydrogen, can drastically reduce the carbon footprint of steel production. Green hydrogen is seen as a game-changer, although it is currently limited by high costs and infrastructure requirements [5].
- Energy Efficiency Improvements: Implementing advanced technologies and optimizing processes can reduce the energy required per ton of steel produced, thus lowering emissions [4].
- Carbon Capture, Utilization, and Storage (CCUS): This technology involves capturing CO2 emissions from steel plants and either storing them underground or using them in other industrial processes. While promising, CCUS is still in the initial stages of commercial viability and requires significant investment. Global CCUS investment requires a US $196Bn investment through 2024 [13].
The Story of Cost
While the use of the above technologies will result in near-zero emissions, IEA states that these technologies are between 10% and 50% more expensive than their commercially available counterparts, making the switch economically unattractive.
Consider the case of H2-DRI. Hydrogen from renewable sources currently costs $4.5 – $6.5 per kg, while fossil fuel-based hydrogen is $0.5 – $1.7 per kg. By 2030, renewable hydrogen costs are expected to fall to $2.5 – $4.0 per kg and in regions with excellent renewable sources, as low as $1 per kg by 2050. This could make green steel cost-competitive (read: affordable). What is also promising is that IEA’s database on Hydrogen Projects shows 1000+ new projects added (in concept or feasibility study) which confirms that hydrogen from renewable electricity could fall by 30% by 2030 owing to the scaling up of hydrogen production and declining costs of renewable energy overall. [20, 21]
To put this into perspective, consider the industry that has the most steel usage at 52% – construction and infrastructure. Transition Asia estimates, in China, at a hydrogen cost of $5/kg, the green premium for steel amounts to about $225 per ton. This leads to an additional $563 for a 50 m² residential unit (assuming 50 kg of steel per m²), a minimal increase in the overall construction cost. However, as hydrogen prices are projected to drop to around $1/kg, this green premium could be virtually eliminated. [23]
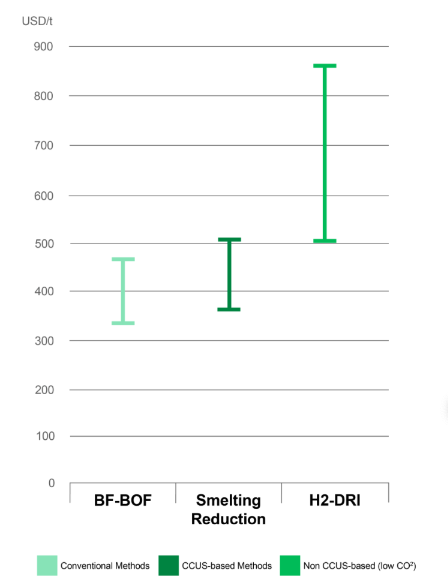
Fig.3 Comparison of costs of producing steel from different methods: BF-BOF, Smelting Reduction, and H2-DRI
European Initiatives and Regulatory Support
Quite a few European regulatory initiatives and public policies have been outlined to support the decarbonization of the steel industry. Specifically, the European Green Deal sets out a roadmap to achieve net-zero greenhouse gas emissions by 2050, with interim targets to reduce emissions by 55% by 2030. The Deal’s Fit for 55 package includes revisions to existing regulations and introduces new measures, such as more ambitious binding annual targets for renewable energy use and energy efficiency, directly impacting the steel sector by pushing for cleaner production methods [12]
- Carbon Border Adjustment Mechanism (CBAM): Set to take full effect by 2026, CBAM is designed to prevent carbon leakage by imposing a carbon tax on imports of carbon-intensive goods, including steel. This regulation incentivizes EU steel producers and the outside producers of EU imported products to reduce emissions and adopt greener technologies, as the cost of non-compliance will increase over time [11]
- State Aid for Green Steel Projects: The European Commission has approved various state aid measures to support green steel projects across Europe. For instance, a €280 million Belgian measure and a €460 million Spanish measure were recently approved to support the development of green steel production. These funds are directed toward innovative projects that aim to replace fossil fuels with renewable hydrogen in steelmaking processes [12]
- REPowerEU and EU Hydrogen Strategy: These initiatives focus on accelerating the adoption of hydrogen as a key energy source in decarbonizing heavy industries like steel. The European Clean Hydrogen Alliance, established under the EU Hydrogen Strategy, aims to facilitate large-scale hydrogen projects, including those in steel production [12]
Several major steelmakers across the world – like ArcelorMittal and H2Green Steel from Europe, HBIS and JSW from Asia, and Nucor from the Americas, are leading the way in decarbonization efforts, refer to the table at the end to gain into their technology shifts and important partnerships that are helping them achieve the decarbonization and their bold aims with using green electricity citing the key role electricity plays in these efforts
Major Steelmakers and their green ecosystem [22]
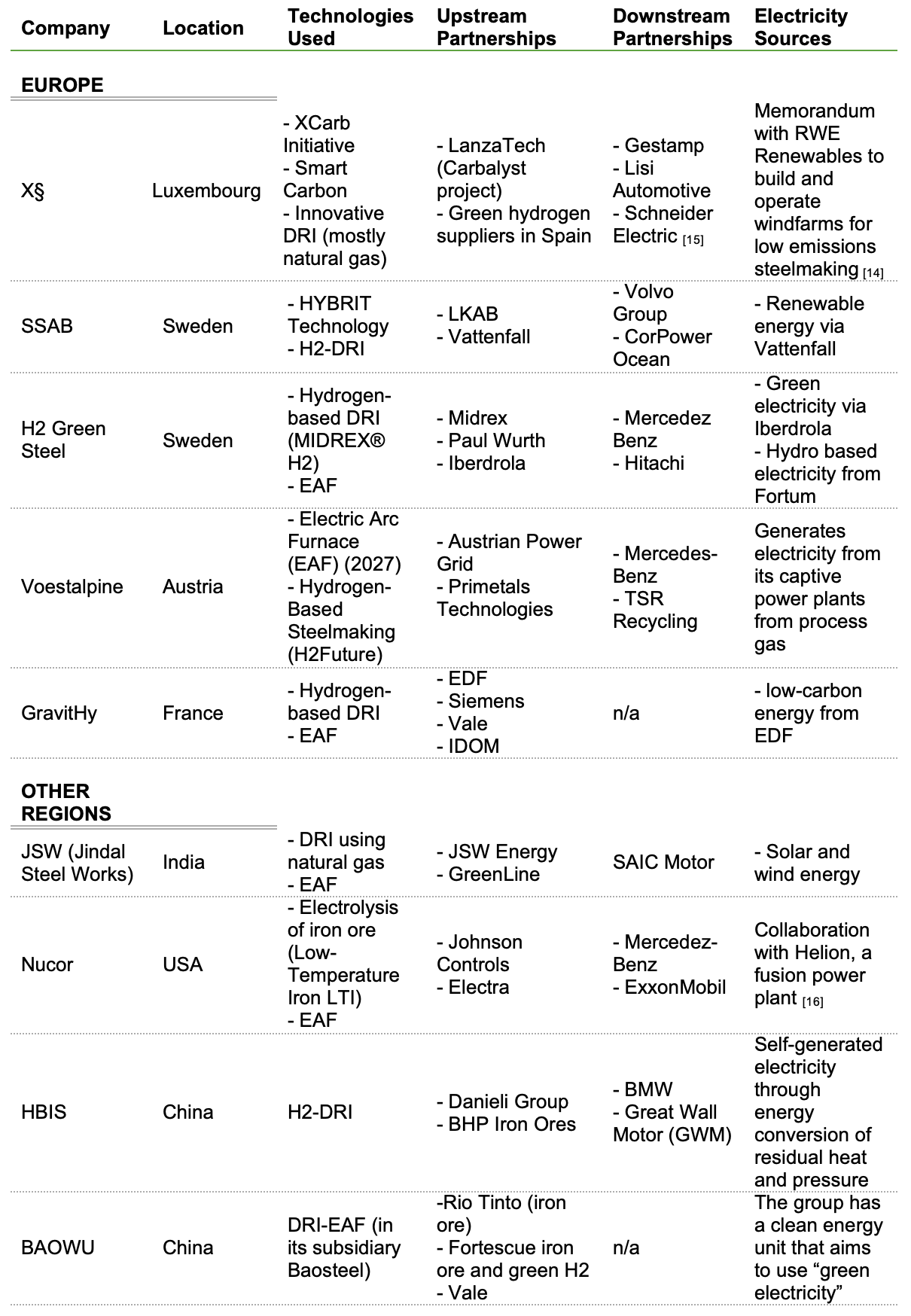
These initiatives require significant capital expenditure (CAPEX). For instance, the HYBRIT project alone is estimated to cost over €2 billion [6]. To support these efforts, both public funding and private investment are crucial. [2].

SOURCES
- ArcelorMittal. (2023). Climate Action Report 2023.
- European Commission. (2023). Carbon Border Adjustment Mechanism.
- Franklin Templeton. (2023). Green Steel: The Industry’s Path to Net Zero.
- International Energy Agency: Iron and Steel Technology Roadmap
- ScienceDirect. (2022). Low Carbon Steelmaking Technologies. Retrieved from https://www.sciencedirect.com/science/article/abs/pii/S2214629622000706.
- SSAB. (2023). HYBRIT: Fossil-Free Steel Production. Retrieved from https://www.ssab.com/company/sustainability/sustainable-offering/hybrit.
- Thyssenkrupp. (2023). Our Path to Carbon Neutrality. Retrieved from https://www.thyssenkrupp.com/en/company/sustainability/climate-action.html.
- World Economic Forum. (2022). Green Steel: Emissions and Net Zero. Retrieved from https://www.weforum.org/agenda/2022/07/green-steel-emissions-net-zero/.
- World Economic Forum. (2023). Why Steel Can Be an Unexpected Leader in Decarbonization. Retrieved from https://www.weforum.org/agenda/2023/08/why-steel-can-be-an-unexpected-leader-in-decarbonization/.
- World Steel Association. (2024). World Steel in Figures https://worldsteel.org/wp-content/uploads/World-Steel-in-Figures-2024.pdf
- https://www.se.com/ww/en/about-us/newsroom/news/press-releases/schneider-electric-partners-with-arcelormittal-on-low-carbon-steel-to-reduce-the-environmental-impact-of-its-products
- Approximation from source reports of ADEME, IEA, Fraunhofer, World Steel Association, and RMI
- Jinsoo Kim, Benjamin K. Sovacool, Morgan Bazilian, Steve Griffiths, Junghwan Lee, Minyoung Yang, Jordy Lee, Decarbonizing the iron and steel industry: A systematic review of sociotechnical systems, technological innovations, and policy options, Energy Research & Social Science, Volume 89, 2022,102565, ISSN 2214-6296, https://doi.org/10.1016/j.erss.2022.102565. (https://www.sciencedirect.com/science/article/pii/S2214629622000706)
- World Steel Association https://worldsteel.org/publications/policy-papers/climate-change-policy-paper/
- Hydrogen Council Insights https://hydrogencouncil.com/en/hydrogen-insights-2023-december-update/
- DWDG Analysis.
- Green Steel Economics Report. Transition Asia.