L’initiative du “Passeport Batterie” de l’Union Européenne (nouveau règlement sur les batteries) vise à renforcer la durabilité de la production et de l’utilisation des batteries à travers l’UE. Cette initiative se concentre sur l’amélioration de la traçabilité des matériaux utilisés dans les batteries et encourage le recyclage de composants tels que le nickel et le cobalt. D’ici 2027, toutes les batteries pour véhicules électriques (VE) et batteries industrielles sur le marché européen devront être dotées d’un passeport batterie unique, identifié par un QR code. Ce passeport fournira des informations détaillées sur l’origine et le cycle de vie des matériaux, favorisant ainsi les pratiques d’économie circulaire.
La production de nickel est l’une des étapes les plus émettrices de gaz à effet de serre (GES) dans la fabrication des batteries, représentant en moyenne un tiers des émissions totales pour les batteries riches en nickel. Le rôle de l’Indonésie, en tant que premier pays producteur et raffineur au monde, avec un processus de production hautement polluant, sera central dans la décarbonation des batteries.
Ainsi, il sera essentiel de trouver un équilibre entre une nouvelle production durable et des stratégies solides de recyclage, y compris des initiatives comme le Passeport Batterie, pour naviguer dans les complexités du marché en évolution du nickel et soutenir la transition vers une énergie propre.
Le nickel améliore les performances des batteries mais fait grimper leurs émissions de carbone
La croissance exponentielle de la production de véhicules électriques (VE) dans le monde redessine l’économie mondiale, notamment en ce qui concerne les besoins en matières premières. Au cœur de ce changement se trouve l’explosion de la demande de nickel, un composant clé des batteries de VE. En 2023, les ventes mondiales de VE ont frôlé les 14 millions d’unités, soit 18 % de toutes les voitures vendues, marquant une augmentation de 35 % par rapport à l’année précédente, et cette tendance ne montre aucun signe de ralentissement. Selon différents scénarios, l’Agence Internationale de l’Énergie (AIE) prévoit qu’en 2030, les ventes de VE représenteront entre 40 et plus de 60 % de toutes les ventes de voitures neuves dans le monde. Cette augmentation est directement liée à un besoin croissant de nickel dans la production de batteries, en raison de son rôle dans les batteries à haute densité énergétique qui alimentent ces véhicules.
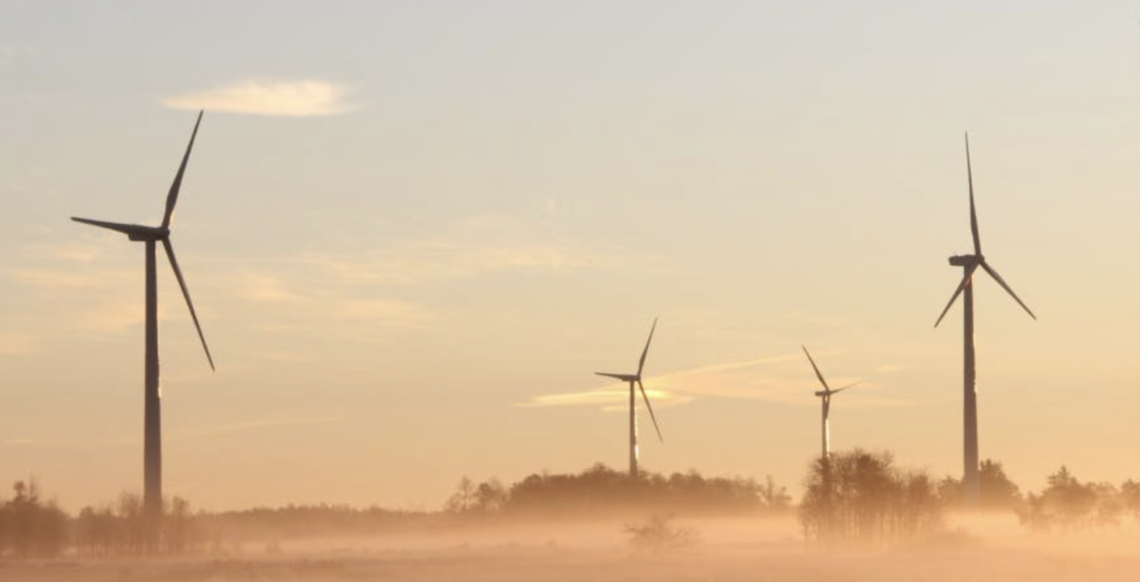
Le nickel est en effet un élément clé des batteries modernes de véhicules électriques (VE), en particulier dans le développement de chimies de batteries à haute densité énergétique. Parmi les deux types de batteries les plus courants sur le marché des VE, les batteries au phosphate de fer lithium (LFP) (part de marché de 40%) et les batteries au nickel manganèse cobalt (NMC) (part de marché de 57%)4, ces dernières dominent en raison de leur densité énergétique supérieure et de leur capacité de stockage. Les batteries NMC sont privilégiées en Europe et en Amérique du Nord, où la demande pour des VE à grande autonomie est plus forte. L’évolution des batteries NMC, de NMC 111 (contenant des proportions égales de nickel, manganèse et cobalt) à NMC 811 (avec huit parties de nickel pour une partie de manganèse et de cobalt), souligne l’importance croissante du nickel. Ce changement est motivé par la nécessité de réduire la dépendance au cobalt coûteux tout en améliorant les capacités de stockage d’énergie.
L’utilisation du nickel dans les batteries améliore considérablement la densité énergétique, en faisant un composant crucial pour augmenter l’autonomie des VE, réduire les coûts par kilowatt-heure et améliorer les performances globales des batteries5. Les batteries riches en nickel ont une densité énergétique d’environ 150 à 220 Wh/kg, soit presque le double des batteries LFP, qui ont une densité énergétique de 90 à 120 Wh/kg6.
Pour la production de batteries, seul le nickel de haute pureté est adapté. Ce type de nickel provient principalement de deux types de minerais : les sulfures et les latérites. Les minerais sulfures, bien qu’ils soient plus faciles à traiter, sont relativement rares et leur disponibilité est en diminution. En revanche, les minerais latérites sont plus abondants, notamment dans des régions comme l’Indonésie, mais nécessitent un processus d’extraction énergivore et environnementalement difficile, appelé High-Pressure Acid Leaching (HPAL). Le Nickel Pig Iron (NPI) peut être transformé en nickel matte pour produire du nickel de haute pureté, bien que son utilisation reste limitée, car le NPI est généralement un produit flexible entre les applications acier inoxydable et batterie. Par conséquent, la principale matière première pour la production de nickel de haute pureté passe progressivement des minerais sulfureux aux minerais latéritiques.
Cependant, à mesure que l’industrie cherche à réduire l’impact environnemental des batteries lithium-ion, l’attention se porte souvent sur le nickel en raison de sa contribution significative aux émissions de gaz à effet de serre (GES). Par exemple, dans une batterie NMC811, qui utilise une proportion élevée de nickel, les émissions totales de GES associées à sa production sont estimées à environ 77 kg CO2eq par kWh de capacité de stockage. Ce chiffre inclut les émissions provenant des étapes minières, de traitement des matériauxet de fabrication. De manière cruciale, de ce total, 25 kg CO2eq par kWh — soit environ un tiers — provient directement de la production de sulfate de nickel. Cela fait de la production de nickel un point de levier important pour réduire les émissions globales liées aux batteries.
Un rôle central pour l’Indonésie, qui continuera de croître, malgré un processus de production deux fois plus polluant que la moyenne de l’industrie
En 2022, la demande mondiale de nickel a atteint 3 millions de tonnes métriques, avec plus de 60% de la consommation destinée à la production de acier inoxydable9, tandis que la demande pour les batteries représentait environ 16% de la consommation totale de nickel. Cependant, la croissance rapide du secteur des véhicules électriques (VE) a entraîné une augmentation sans précédent de la demande de nickel de qualité batterie : le segment des batteries est passé de 4% en 2010 à plus de 15% ces dernières années.
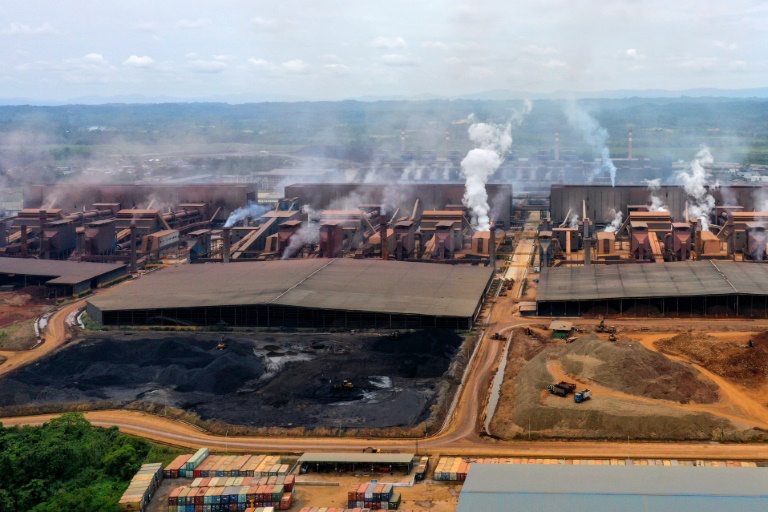
La production de nickel est concentrée dans quelques régions clés, l’Indonésie et la Chine étant les principaux producteurs. L’Indonésie, qui détient les plus grandes réserves de minerai de nickel latéritique, a connu un afflux massif d’investissements ces dernières années dans le cadre de sa stratégie nationale pour devenir un hub mondial de production de nickel. En 2022 seulement, l’Indonésie a produit 1,6 million de tonnes métriques de nickel, représentant plus de 49% de la production mondiale10. Le raffinage est, pour l’instant, plus diversifié, avec l’Indonésie représentant 38,4% de la part mondiale, la Chine 27,4% et la Russie **4,7%**11. Cependant, les coûts environnementaux sont considérables. Les processus de raffinage du nickel en Indonésie figurent parmi les plus intensifs en carbone au monde. Le pays dépend largement de l’électricité provenant du charbon, ce qui augmente considérablement l’empreinte carbone de la production de nickel. Une comparaison de six routes de production de sulfate de nickel révèle que les niveaux d’émissions des installations les plus performantes, situées au Canada et en Finlande, sont respectivement 70% et 63% inférieurs à la moyenne de l’industrie de 18 kg CO₂ par kg de nickel dans le sulfate de nickel12. En revanche, la route de l’acide à haute pression (HPAL), de plus en plus populaire en Indonésie, produit presque deux fois plus d’émissions que la moyenne de l’industrie, avec 36,8 kg CO₂-eq par kg de nickel. Le traitement des minerais latéritiques en Nickel Pig Iron (NPI), puis sa conversion en matte et enfin en sulfate de nickel, produit des émissions cinq fois supérieures à la moyenne de l’industrie13. Cela représente un défi environnemental majeur à mesure que la demande de nickel continue de croître.
Le rôle de l’Indonésie dans la production de nickel devrait continuer à se développer considérablement d’ici 2030, grâce à ses vastes réserves de minerai latéritique et à l’augmentation de sa capacité de raffinage. L’Indonésie devrait représenter environ 60% de l’extraction mondiale de nickel et 45% de la capacité de raffinage de nickel d’ici 203014. Depuis la réimposition d’un interdiction des exportations de nickel brut en 2020, le pays s’est concentré sur le développement d’une industrie de raffinage nationale, attirant des milliards de dollars d’investissements de la part d’entreprises chinoises et occidentales15. L’impact environnemental élevé de l’extraction du nickel latéritique a conduit à des appels en faveur de régulations environnementales plus strictes et du développement de technologies plus propres. Actuellement, l’Indonésie présente également le taux de déforestation lié à l’exploitation minière le plus élevé au monde16 : L’exploitation minière du nickel en Indonésie a entraîné la déforestation de jusqu’à 153 364 hectares de forêts dans les limites des concessions de nickel de l’Indonésie depuis 2000. À Sulawesi, 36% des terres forestières sont occupées par des concessions de nickel, menaçant la biodiversité et réduisant la capacité de puits de carbone des forêts17.
De plus, la production d’électricité à base de charbon représente encore environ 60% de la part de la production d’énergie18. Le pays prévoit d’augmenter sa capacité de production d’énergie à partir du charbon : à la fin de 2022, l’Indonésie avait 18,8 gigawatts de centrales à charbon en construction. Notamment, 69% (soit 13 GW) de ces nouvelles centrales seront “captives”, dédiées à alimenter des consommateurs industriels et commerciaux plutôt que le réseau électrique19. Cela comprend des installations pour la fusion de l’aluminium et le traitement du nickel et du cobalt. Cette dépendance à des méthodes de production intensives en GES reste un obstacle majeur à l’atteinte des objectifs climatiques mondiaux.
Le chemin à suivre : répondre à la demande croissante de nickel grâce au recyclage, au développement de nouveaux procédés et à l’utilisation des énergies renouvelables
Le développement futur du nickel est alimenté par une augmentation prévue de la demande, avec des estimations indiquant que la demande mondiale de nickel pourrait atteindre 4,2 millions de tonnes métriques d’ici 2030,20 principalement en raison du secteur des VE, si les batteries NMC restent le type dominant, mais aussi en raison de la demande croissante en acier inoxydable. Cette demande nécessite des expansions significatives de la capacité de production. Cependant, la dépendance à l’Indonésie présente des risques géopolitiques liés à la stabilité de l’approvisionnement, notamment en raison de changements réglementaires potentiels, de la lutte contre la corruption et des préoccupations environnementales.21
Pour atténuer ces risques, les acteurs de l’industrie doivent prioriser les efforts de recyclage. Le processus de recyclage des batteries lithium-ion comprend trois étapes principales : prétraitement, extraction des métaux, et séparation des produits. Lors du prétraitement, le boîtier de la batterie est retiré et les matériaux de la cathode sont séparés. Deux méthodes industrielles principales sont utilisées ici : la pyrométallurgie, qui peut traiter diverses chimies en un seul processus, et le traitement mécanique, plus sensible à la contamination et nécessitant un démontage et un tri. Les processus manuels ou semi-automatisés sont courants en raison des coûts élevés de l’automatisation. L’extraction des métaux repose généralement sur la pyrométallurgie, l’hydrométallurgie, ou la biomineralisation, l’hydrométallurgie étant la méthode préférée pour récupérer des métaux comme le lithium et le cobalt via des solutions acides et des agents réducteurs. Enfin, la séparation des produits est réalisée par précipitation sélective, extraction par solvant, ou électrodialyse. Bien que l’hydrométallurgie nécessite moins d’énergie que la pyrométallurgie et ne produise pas de gaz dangereux, elle génère des déchets dangereux, signalant une marge d’amélioration pour le recyclage des LIB. En conséquence, les émissions Scope 1 et Scope 2 combinées sont significativement plus élevées pour une route Mech-Pyrolisis-Hydro (0,8 kg CO2e/kg équivalent module) que pour un processus Mech-Hydro (0,3 kg CO2e/kg équivalent module), mais l’écart se réduit lorsqu’on prend également en compte le Scope 3 (respectivement 2,6 et 2,3 kg CO2e/kg équivalent module).23
Certaines études indiquent que le recyclage des batteries lithium-ion usagées peut récupérer 95% des métaux,24 réduisant ainsi considérablement le besoin de nouvelles extractions minières. Les technologies de recyclage améliorées pourraient garantir que le recyclage annuel du nickel pourrait couvrir entre 67,7 % et 96,6 % de la demande de batteries de VE en Chine en 2050, selon les scénarios.25 C’est plus que nécessaire, étant donné que, selon le “Battery Passport” de l’UE, les batteries doivent contenir un minimum de 16 % de cobalt, 85 % de plomb, 6 % de lithium, et 6 % de nickel provenant de sources non vierges d’ici 2031. Cependant, les batteries sont des produits durables, et le recyclage ne sera pas la principale réponse pour les dix prochaines années d’approvisionnement.
Parmi les diverses stratégies de décarbonisation, passer à des sources d’énergie renouvelables ou faibles en carbone peut réduire les émissions de jusqu’à 40% en moyenne dans la production de nickel.26 D’autres stratégies essentielles pour atténuer les émissions de gaz à effet de serre (GES) incluent l’utilisation de produits chimiques zéro carbone pendant le traitement, le chauffage électrique, la décarbonisation des véhicules miniers, et l’optimisation des logistiques. Pour la production de Nickel Classe 1 à partir de HPAL, le modèle IFC propose les options de la manière suivante27 :
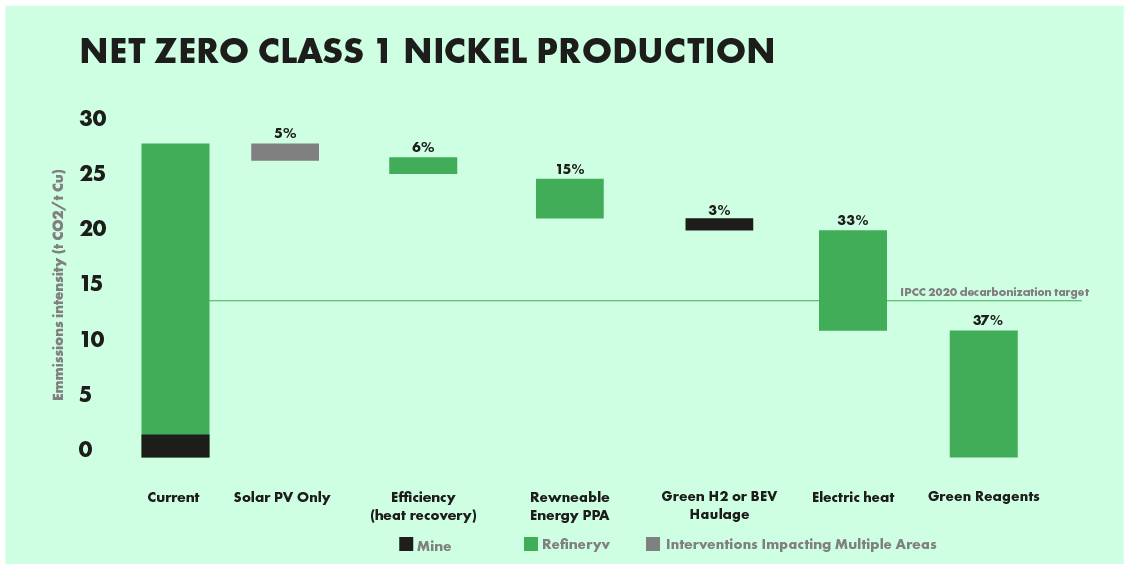
De plus, l’adoption de techniques de traitement des minerais plus énergétiques efficaces est essentielle. Pour les minerais sulfurés, l’extraction bioheap et l’oxydation sous pression peuvent réduire les besoins en énergie, tandis que pour les minerais latéritiques, l’extraction en tas et le traitement hydrométallurgique atmosphérique sont des solutions clés pour réduire l’empreinte carbone globale de l’industrie. Par exemple, la production de nickel par exploitation minière en mer profonde via la collecte de nodules par TMC Miningest censée surpasser non seulement le nickel indonésien, mais également toutes les autres principales méthodes de production terrestre, avec une réduction moyenne des émissions de 70-80%.28 Cependant, les effets indirects et les risques de l’exploitation minière en mer profonde doivent être pris en compte, tels que la déstabilisation des océans, l’extinction des espèces, la destruction des habitats, et les impacts sur la sécurité alimentaire mondiale.29
De la mine à la route : comment le nickel propulse la révolution des VE (Véhicules Électriques)
En conclusion, le chemin vers la décarbonisation des batteries et l’atteinte de la durabilité dans le secteur des véhicules électriques (VE) est complexe et semé d’embûches. Le nickel joue un rôle central dans cette transition, étant essentiel pour les batteries de haute performance, mais sa production est actuellement liée à des émissions importantes de gaz à effet de serre et à une dégrégation environnementale, notamment en Indonésie. L’initiative Passport Batterie de l’UE vise à répondre à ces préoccupations en améliorant la traçabilité des matériaux et en promouvant le recyclage, établissant une norme pour une approvisionnement responsable. Cependant, à mesure que la demande de nickel devrait continuer à augmenter, une approche multifacette est nécessaire—équilibrer la nécessité de nouvelle production avec des stratégies de recyclage robustes et l’adoption de technologies plus propres. Bien que des avancées telles que l’intégration des énergies renouvelables et des techniques innovantes de traitement des minerais offrent des voies prometteuses pour réduire les émissions, le chemin à parcourir reste long. Atteindre une chaîne d’approvisionnement de batteries durable nécessitera une collaboration entre les industries, des cadres réglementaires et des innovations technologiques pour s’assurer que les avantages de la révolution des VE ne se fassent pas au détriment de notre environnement. L’engagement envers la décarbonisation doit être inébranlable alors que nous naviguons dans cette transition essentielle vers un avenir plus propre.
Retrouver d’autres articles ici.
2 PNAS Nexus, “Estimating the environmental impacts of global lithium-ion battery supply chain: A temporal, geographical, and technological perspective”, 2023
3 IEA, Global EV Outlook 2024, 2024
4 ibid
5 Nickel Institute, “How nickel makes electric vehicle batteries better” 2023
6 Mayfield Energy, 2023
7 Roskill for the European Commission, “Study on future demand and supply security of nickel for electric vehicle batteries”, 2021
8 PNAS Nexus, “Estimating the environmental impacts of global lithium-ion battery supply chain: A temporal, geographical, and technological perspective”, 2023
9 BGR, “The importance of Indonesia for the global nickel market”, 2024
10 IEA, Global Critical Minerals Outlook 2024
11 BGR, “The importance of Indonesia for the global nickel market”, 2024
12 Transport & Environment, Paving the way to cleaner nickel, 2023
14 IEA, Global Critical Minerals Outlook 2024
15 Center for Strategic & International Studies, 2021
16 WWF, Extracted Forests, 2024
17 Mighty Earth, “Sourcing responsible nickel for Evs” 2023
18 IESR, Indonesia Energy Transition Outlook 2023, 2023
19 GEM, 2023
20 IEA, Global Critical Minerals Outlook 2024
21 Trytten, Lyle, Will Cheap Asian HPAL Save the EV Industry from its Looming Success? 2020
22 Resources, Conservation and Recycling, 2022
23 Umicore’s Calculations
24 Redwood Materials, 2023
26 Transport & Environment, Paving the way to cleaner nickel, 2023
27 IFC, “NET ZERO ROADMAP TO 2050 For Copper & Nickel Mining Value Chains”, 2022
28 Benchmark Mineral Intelligence, LCA, 2022
29 African Mining Review, 2024